CASS IN THE NEWS!
CASS Custom Architectural Sheetmetal Specialists - Detroit, MI
NEWS ARTICLE - CAM Magazine - Read the full story below.
Landmark Historical Building Roof Restoration & Preservation
Cranbrook Institute - Kingswood School New Copper Roofing
Historic National Landmark Building - Copper Roofing Replacement by CASS Sheetmetal - Detroit, MI
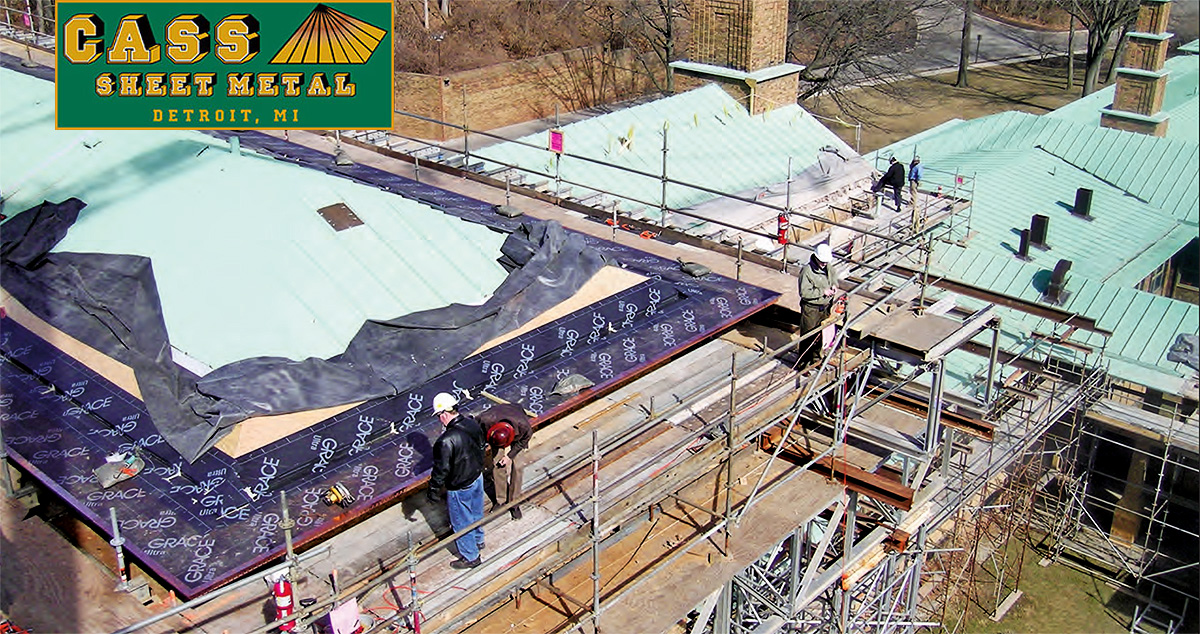
Project Overview - Highlight Photos by CASS
A Penny Saved is a Reputation Earned!
When most people think of copper, they tend to think about coin change in their pockets as opposed to roofs above their heads. While copper is still used in roofing today, the material has lost ground to less extensive alternatives, and many of the most dramatic copper applications sit atop older buildings as prominent reminders of the craftsmanship of a bygone era. An ambitious attempt to resurrect the splendor of the past is exactly what CASS Sheetmetal did to the roof of Kingswood School on Cranbrook’s National Historic Landmark campus in Bloomfield Hills, MI.
At nearly 90,000 square feet, the copper roof at Kingswood School is one of the largest in the United States, but its structural integrity had degraded over time. Without corrective action, water intrusion would slowly erode the venerable structure designed by Eliel Saarinen. Following the completion of an initial roof replacement (30,000 square feet) by the owner in 2001, the design/build team divided the remainder of the project into three work areas. The first area, where the initial work began covered the roofing over the dining hall, auditorium, common room and old ballroom. For roofing contractor, CASS Custom Architectural Sheetmetal Specialists, Inc. a copper roof saved is a reputation earned at the completion of this enormous project.
COPPER AND TIME
Kingswood School, completed in 1931, is a true architectural gem well worth preserving, and the copper roof is a vital building element. Eliel Saarinen selected copper for the Kingswood roof because copper in its natural state harmonized nicely with the building’s buff brick and Mankato limestone walls. As the copper weathered, it harmonized with the horizontal building accents of green brick and the foliage of the site.
“Kingswood School at Cranbrook is one of the best examples of early modern school architecture,” said Paul Darling, AIA, senior project manager for QE I A.“The batten seam roofing is a defining feature of the building design. The broad overhangs and the two-sloped eave emphasize the horizontal plane and tie the building into the surrounding landscape. Strong vertical building elements and chimneys break the roof plane. The roof battens extend over the ridge and hips, creating a ‘saw-toothed’ appearance.”
For 75 years, the copper roof provided shelter while creating a distinctive look for Kingswood.Over time, the daily pounding of the elements has taken a toll.
“The biggest problem with copper roofs is expansion and contraction,” said Fred Spencer, Jr., senior project manager for Skanska USA Building Inc. “Copper has a very high coefficient of expansion. When you go from the dead of winter to summer heat, you are talking about a 170ºF temperature difference on a copper roof. A 50-foot length of copper will walk about an inch, and you need to accommodate that. The problem with the old building roof is that it basically tore itself apart in certain areas.” Fortunately for Kingswood School, no firm is better qualified to pick up the pieces of the battered roof system than C.A.S.S. Few companies have amassed as much knowledge of how metal roof systems react under different conditions.
“Roof systems expand and contract differently,” said Glenn Parvin, president of C.A.S.S. “A flat seam deck is fixed with clips. It is designed to expand within the pan system. Standing seam panels, once they are seamed together, expand longitudinally and horizontally across the base of the pan.” Since Kingswood School features a combination of flat and batten seam roofing, an intricate understanding of how each system performs was necessary for project completion. Tying these roof systems into the existing internal roof drain lines using an internal gutter was even more complicated because the metal gutters expand and contract longitudinally.
Those who are familiar with copper roofing also realize that the material takes on a green patina over time. Many who saw the Kingswood School roof in recent years may have mistakenly attributed the green color to this process, but the appearance is actually caused by a urethane coating that was applied in 1988 to address roof and gutter leaks. “It didn’t solve the problem,” said Spencer. “They basically just put a Band-Aid on the problem.”
While the coating extended to useful life of the old roof by ten years, the urethane spray failed to fix the leaks. Also, overspray created an unattractive residue that is being meticulously cleaned off the adjacent bricks by Skanska USA. Developing solutions that would work without compromising the historic integrity of the building required expert input from the entire project team.
“Probably the biggest challenge on this project was taking our knowledge of best building practices and overlaying it on this uniquely designed existing building,” said Darling.“The articulation of the existing roof edge, with large concrete, copper-clad cantilevers, and the location of the concealed rainwater conductors meant coming up with some creative solutions.”
Many who saw Kingswood School in recent years may have mistaken the color of the existing roof (left) for the green patina that copper takes on over time, but the appearance was actually caused by a urethane coating. New copper (right) looks like a shiny penny.C.A.S.S. outsourced the production of 4,000 LF of ornamental copper fascia, thereby preventing an additional investment in stamping equipment that the company would rarely, if ever, use again.
The end result of all this planning and execution should introduce many of the advantages associated with modern construction methods into a new roof system that will look perfectly natural on the decades old structure.
Before with Old Leaky Copper Roofing
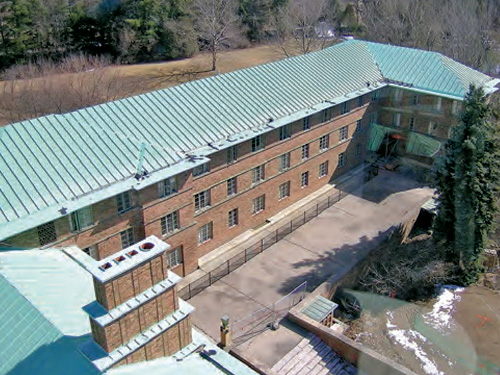
After with New Copper Roofing Replacement
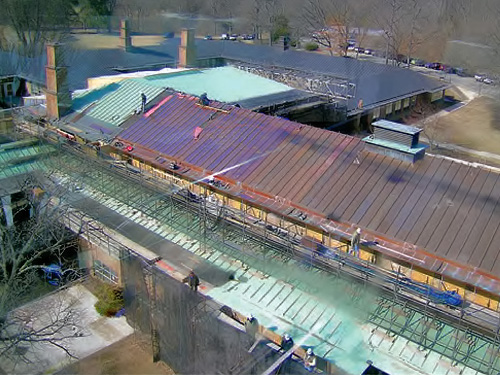
Many who saw Kingswood School in recent years may have mistaken the color of the existing roof (left) for the green patina that copper takes on over time, but the appearance was actually caused by a urethane coating. New copper (right) looks like a shiny penny.
NOT SO FAST FORWARD
C.A.S.S. outsourced the production of 4,000 LF of ornamental copper fascia, thereby preventing an additional investment in stamping equipment that the company would rarely, if ever, use again.
Building a copper roof that would perform better than the original while looking nearly identical was a difficult task. The existing copper roof was slowly tearing itself apart under the stress of temperature extremes because the original design of the gutters and eaves lacked sufficient expansion capabilities. Expansion joints were added to these key areas of the roof to remedy this problem. The original roof design also concealed an elaborate drainage system of internal gutters and rainwater collectors located within the walls. In order to divide the gutters into shorter sections between the expansion joints, more downspouts were needed.
“An easy fix would be to just add downspouts,but we would have compromised the architectural value of the building,” said Spencer.“Since the building design is of critical importance,we opted to add six downspouts in inconspicuous areas. We also have 12 new internal roof conductors. With some, we created a new outlet and connected them to an existing roof conductor. There are others that drop right through the building and then out into the storm drainage system.”
The design/build team looked at several options, ranging from draining the water directly to grade and then collecting it, to reconstructing the built-in gutters and repairing the rainwater conductor system. “Our final recommendation was to stay with the built-in gutters and re-use the rainwater conductors,” said Darling. “Interior rainwater collectors have an advantage over downspouts, because heat from the building helps keep them warm and free from ice dams.”
Although this warmth prevents ice dams in interior rainwater conductors, it could cause ice build up on the roof and gutters. Extra insulation and a mechanical ventilation system are being added to create attic temperatures consistent with the outside air, thereby preventing interior heat sources from melting snow on the roof leading to ice dams. In addition to drainage system design, other building practices have changed since the 1930s construction of Kingswood School. Exactly replicating the existing design would have made the project far too expensive to complete, but a few inconsequential changes allowed the project to commence. The French batten caps originally used, for example, featured a square base with a tapered top.
“Matching the exact profile of the batten would have required a hammered seam, or hand folding and hammering the seam throughout the entire job”, said Parvin.“Generally speaking,newer machinery will not work with that type of batten cap”. Parvin worked with the architect and owner to switch to a square batten cap, but one that was only one inch wide to more closely match the original. The non-standard size still presented challenges. “I had to take that request back to the manufacturers of roll forming equipment,” said Parvin. “The equipment wasn’t a shelf item. They could provide the equipment, but it would take 12-16 weeks. I also needed to allocate a lot of money towards these products because I needed a seamer capable of seaming a one-inch-wide wood batten.”
With pan formers typically costing $35,000 to $50,000, plus the $20,000 modification that would be required, plus $10,000 to $15,000 for the seamer, C.A.S.S. incurred significant expenses before the company could count on any financial return.Parvin wisely chose to spread some of the financial risk instead of incurring it all for himself. He outsourced production of 4,000 LF of ornamental copper fascia to AW Zahner, Kansas City, MO, thereby preventing an additional investment in stamping equipment that his company would rarely, if ever, use again.
Some design changes, like the batten caps, were intended to allow for current construction techniques. Modern materials that will not be visible when construction is complete will also enhance the durability of the structure. Ice and water shield membrane, which was not available in the 1930s, will provide an extra layer of protection at eaves, peaks, gutter boxes and valleys.Any water that accumulates on the ice and water shield membrane will flow down into the gutter boxes and be collected and drained out via small drip tubes through the soffit. The copper roof will also conceal stainless steel fittings that will cover electrical heat tapes. These tapes will drop down into the gutters, where they will melt ice and snow.
“We also used a new technology to repair the existing cast iron rainwater conductors,” said Darling. “A fabric-reinforced resin-soaked liner was inserted into each one, and an inflatable bladder was inserted, inflated, and then removed once the resin sets. This will extend the life of the drainage system for another 75 years.”
Blending contemporary materials and techniques with the craftsmanship of yesteryear required workers with a high degree of skill.
PERFORMANCE TIME
Soldering of gutters and flat seam roofing was a vital part of the project at Kingswood School. Since any imperfections could result in a leak, the ownerinsisted on certifying every worker who would perform the delicate operation. Every month, each worker is required to submit a work sample called a “soldering coupon”. The quality of the solder on each sample is carefully inspected, and only those who pass the inspection are permitted to perform the work. This quality requirement put C.A.S.S. in an unusual situation.
“Soldering is becoming a lost art,” said Parvin. “People got away from soldering day in and day out, so a lot of the true craftsmen are the older tinsmiths. The talent level that was needed out here couldn’t just be pulled off the shelf. On a 25-man crew, there are probably five to eight who could potentially pass all of the criteria to be entitled to work out here, and all of those people are C.A.S.S. foremen. We can’t bid, quote, and sell a job as if we are shutting our entire operation, because we still need to serve our other clients.”
After meticulously evaluating the skills of the C.A.S.S. workforce, Parvin was able to devise a staffing plan that enabled him to put enough highly-skilled craftsmen to work at Kingswood School while still retaining enough qualified foremen to handle other jobs. Staffing was not the only project issue that required careful planning. Kingswood School will be in operation during the project, so the safety of students and staff will be critical. Fortunately, in 2000 Skanska USA Building Inc. launched an inventive new safety program where jobsites are Injury Free Environments (IFE). Kingswood School is a current example of the IFE culture at work. IFE basically enables everyone on the project to contribute to the safety effort. Skanska trains every trade that enters the project so that they too can focus on safety in their job as well as their lives. Every person is encouraged to look out for their safety and the safety of their fellow workers, and they are empowered with the ability to immediately shut down any operation they feel is unsafe. With every eye at the jobsite focused on safety, the goal of an Injury Free Environment is attainable.The injury Free Environment philosophy does not end when you walk off a Skanska jobsite – it is a way of life.
“Our primary goal for every person who comes to work each day is to have that person go home every night in a safe and normal manner,” said Spencer.
Access to the site is also restricted to extend safety benefits beyond just the workers.Netting and plywood are installed to scaffolds and ladders to secure them at the end of the day, and emergency contact numbers facilitate quick contact between school officials and jobsite supervisors if any unauthorized access is evident.
The project team’s thorough planning in regards to safety, as well as all other aspects of the job, virtually assures successful completion.When the copper roof at Kingswood School is complete, the finish will resemble a new copper penny, but its color will gradually change from dull brown to a purplish black before finally settling in on the patina-green hue associated with older structures.The copper will gleam brilliantly during the first few years, but the pride instilled in the project team will undoubtedly last much longer. In this penny saved, reputations will truly be earned.
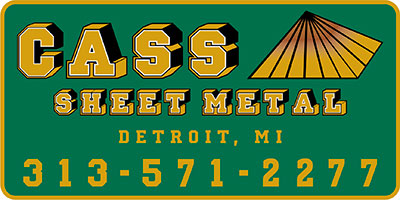
Can One Company Offer So Much? Our Clients Think So!
CASS Sheetmetal Specialists – Detroit, MI (313) 571-2277
Project Consulting, Design/Build, Installation, Custom Fabrication, Standing Seam Copper Domes & Caps, New Construction Standing Seam Metal Roofing, Foam Wall & Stainless Steel Siding Panels, ZInc Siding, Slate & Tiles, Custom Bay Window & Prefab Canopies, Metal Fascias, Soffits & Mansards, Residential Metal Roofing Systems, Historic Building Roof Restoration and More!